In June 2024, Averitt conducted a comprehensive midyear supply chain management survey to gain insights into the challenges faced by shippers when using multiple transportation and logistics providers. The survey reached 989 respondents from small to midsized and enterprise companies across nearly every industry. These individuals primarily work in operations, specifically in logistics and supply chain management, as well as in procurement.
Table Of Contents:
1.) Introduction: Importance of Understanding Your Challenges
2.) The Hidden Costs of Inconsistent Service Quality
3.) The Financial Impact of Fragmented Logistics
4.) Untangling the Web of Logistics Coordination
5.) The Complexity of Handling Multiple Provider Relationships
6.) Overcoming the Tech Hurdle in Logistics Management
7.) Recommendations for Improving Shipper Strategies
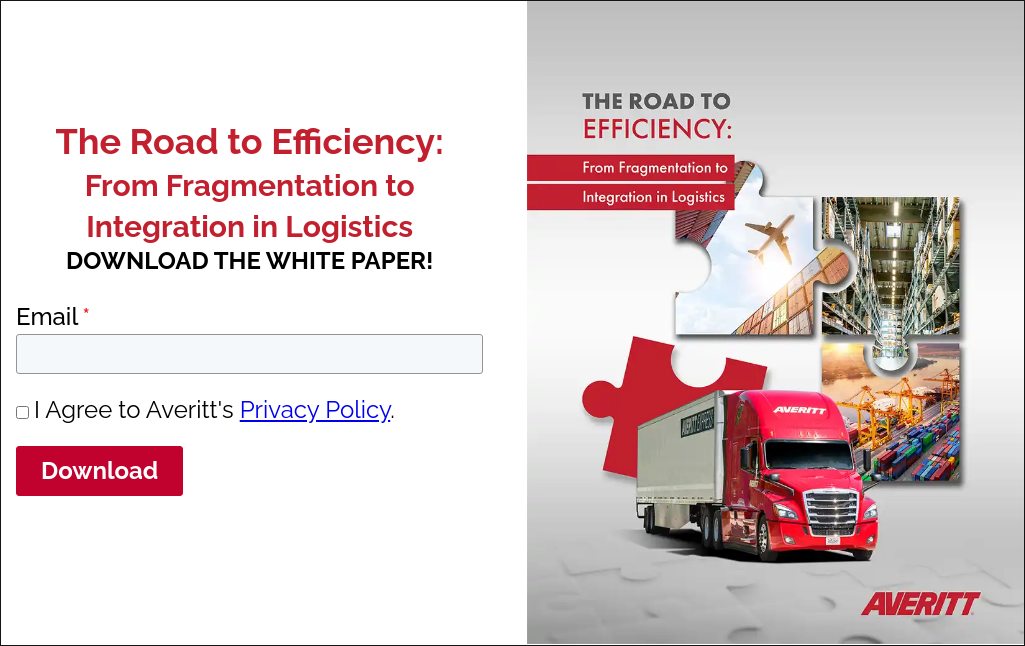
Importance of Understanding Your Challenges
Understanding the complexities and challenges shippers face when managing multiple transportation and logistics providers is crucial. Supply chains are inherently complex, and involving multiple providers increases the chances of breakdowns in communication and operations. These disconnects can occur between each link an organization's operations, leading to inefficiencies and supply chain disruptions.
Relevance to Your Supply Chain
Several trends highlight the importance of addressing these challenges. The rise of technology, cyberattacks, cargo theft, disruptive weather events, the ongoing truck driver shortage, and fluctuations in freight capacity all add complexity to supply chains. Additionally, the shift of international supply chains from China to locales like Mexico, India, and Southeast Asia, coupled with geopolitical challenges, further complicates the landscape.
Insights You’ll Gain
This white paper aims to provide valuable insights into these challenges and offer practical strategies to overcome them. By understanding the pain points and exploring potential solutions, shippers can better navigate the complexities of modern supply chains.
The Hidden Costs of Inconsistent Service Quality
According to the survey, 39.64% of respondents identified inconsistent service quality as their biggest challenge when using multiple transportation and logistics providers. This issue often arises due to varying standards and practices among different providers, leading to a lack of uniformity in service delivery. For instance, while one carrier may offer timely and reliable service, another might struggle with delays and miscommunications. This inconsistency can disrupt the entire supply chain, causing frustration and operational inefficiencies for shippers.
Service Quality Repercussions
The impact of inconsistent service quality is significant. Shippers must navigate the complexities of managing different providers with varying levels of performance. This can result in unreliable delivery schedules, increased costs due to expedited shipments, and, ultimately, a decline in customer satisfaction. When shippers cannot depend on a consistent level of service, it undermines
their ability to plan and execute logistics operations effectively.
Only as Strong as Your Weakest Link
Consider a scenario where a retailer relies on multiple carriers to distribute products nationwide. One carrier may consistently deliver shipments on time, while another frequently encounters delays. This disparity forces the retailer to allocate additional resources to manage late deliveries, potentially resulting in stockouts and lost sales. The inconsistency in service quality creates a ripple effect, impacting the retailer’s overall supply chain efficiency.
To address the challenge of inconsistent service quality, shippers should consider consolidating their logistics providers to streamline operations and ensure a consistent level of service.
The Financial Impact of Fragmented Logistics
According to the survey, 39.53% of respondents reported higher overall costs as a major challenge when using multiple transportation and logistics providers. Managing multiple providers often leads to increased expenses due to fragmented services and lack of economies of scale. Each provider may have different pricing structures, and the cumulative cost of coordinating multiple parties can be substantial.
The Costly Consequences for Shippers
The financial impact of using multiple providers can be considerable. Shippers face higher operational costs, which can erode profit margins. The lack of consolidated pricing and the need to manage multiple
contracts contribute to inefficiencies and increased administrative overhead. Also, shippers may incur additional costs for expedited shipments or resolving issues caused by miscommunications between providers.
A Case in Point
Imagine a shipper in the manufacturing industry that needs to ship products to various distribution and fulfillment centers across the country. By using multiple providers, the manufacturer faces varying rates and surcharges from each provider. This lack of consistency, and even transparency, in pricing can result in higher overall transportation costs and complicates budget forecasting and cost management.
To mitigate higher overall costs, shippers may benefit by consolidating their logistics providers and leveraging integrated solutions.
Untangling the Web of Logistics Coordination
In the survey, 31.75% of respondents identified coordination and communication difficulties as a significant challenge when using multiple transportation and logistics providers. These difficulties arise when shippers must coordinate numerous phone calls and emails to manage shipments across various carriers or try to aggregate and report on information from various technology platforms.
The complexity intensifies when different providers are involved at different stages of the supply chain, such as an ocean forwarder handing off to a drayage company, then to a warehouse company, and finally to an LTL carrier for final mile delivery. This fragmentation can lead to miscommunications and operational breakdowns. Additionally, the use of different technologies by multiple providers can cause delays in data exchange and loss of tracking information.
Operational Strains From Communication Gaps
These coordination and communication difficulties significantly impact shippers. They often spend considerable time calling and emailing various parties to track down the right individuals for answers. This not only consumes valuable time that could be better spent on other critical business areas but also affects operational efficiency. The fragmented communication often leads to delays and inconsistencies, which in turn impact overall customer satisfaction.
The Many Hands Involved
Consider a scenario where a shipper needs to coordinate a shipment from an overseas manufacturer to a local retail store. The shipment involves an ocean forwarder, a drayage company for port handling, a warehouse for interim storage, and an LTL carrier for final delivery. Each of these providers operates on different schedules and systems, requiring constant follow-ups and updates from the shipper. If one link in this chain fails to communicate effectively, it can lead to delays, missed deliveries, and increased costs due to the need for expedited solutions.
Addressing coordination and communication difficulties is crucial for shippers to improve efficiency and customer satisfaction. Streamlining communication channels and integrating technology solutions can help mitigate these challenges.
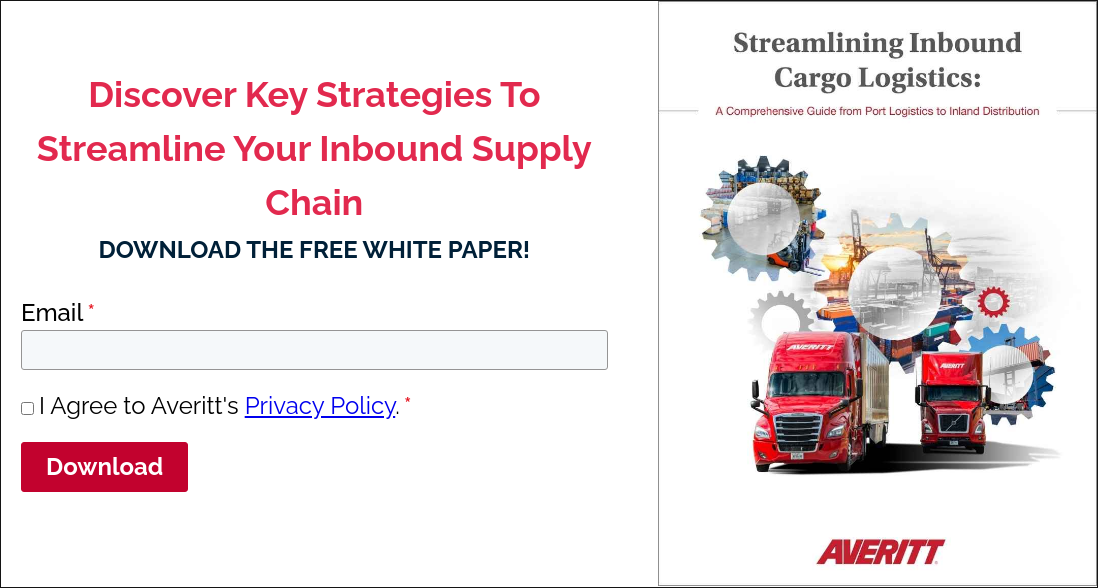
The Complexity of Handling Multiple Provider Relationships
According to the survey, 12.84% of respondents indicated that managing multiple contracts and relationships is a significant challenge when using various transportation and logistics providers. Each provider typically requires separate contracts, and maintaining these agreements can be time-consuming and complex. The challenge is further compounded by the need to nurture relationships with multiple contacts, each with different expectations and communication styles.
Operational Inefficiencies and Administrative Burdens
The difficulty in managing multiple contracts and relationships can lead to several operational inefficiencies. Shippers may experience increased administrative burdens as they juggle different contract terms, renewal dates, and compliance requirements. This complexity can result in missed deadlines, noncompliance with contract terms, and, ultimately, higher operational costs. Furthermore, the need to manage relationships with multiple providers can divert attention from core business activities, impacting overall productivity and effectiveness.
Complex Relationship Management
Imagine a midsized e-commerce company that relies on several logistics providers to fulfill its orders. Each provider requires a unique contract, with specific terms and conditions. The company’s logistics team must keep track of each contract’s details, manage renewals, and ensure compliance. The administrative challenge of managing these contracts, along with maintaining good relationships with each provider, can be overwhelming and detract from strategic initiatives aimed at growing the business.
To mitigate the challenges of managing multiple contracts and relationships, shippers may want to explore consolidating their provider base and leveraging integrated logistics solutions. By doing so, they can streamline administrative processes, reduce costs, and improve overall operational efficiency.
Overcoming the Tech Hurdle in Logistics Management
In the survey, 11.32% of respondents identified the lack of integrated technology solutions as a key challenge when using multiple transportation and logistics providers. Each provider often operates its own technology platform, resulting in a fragmented system where data is siloed and not easily accessible across the supply chain. This fragmentation can hinder real-time visibility and effective decision-making, as shippers must manually consolidate data from different sources.
Consequences of Unintegrated Systems
The lack of integrated technology solutions can significantly impact shippers by reducing operational efficiency and increasing the likelihood of errors. Without a unified system or the use of providers that use modern data streams (EDI, API, etc.), shippers may struggle to gain visibility into their shipments, making it difficult to track progress and anticipate issues. This can lead to delays, increased costs, and lower customer satisfaction. Additionally, the manual effort required to integrate data from multiple systems can divert resources from other critical business functions.
An Example of Coordination Challenges in Manufacturing
Consider a manufacturing company that uses different providers for various stages of its supply chain. The company’s ERP system is not integrated with one service provider’s system, requiring manual data entry and reconciliation. This one gap in visibility can lead to delays in updating shipment statuses, difficulty in tracking inventory levels, and challenges in coordinating production schedules with delivery timelines. The inefficiencies resulting from these manual processes can lead to production delays and increased costs.
To overcome the challenge of lacking integrated technology solutions, shippers may wish to examine opportunities to adopt unified technology platforms that provide end-to-end visibility across the supply chain. Integrated solutions can enhance data accuracy, improve decision-making, and drive operational efficiencies.
Recommendations for Improving Shipper Strategies
Having identified the key challenges faced by shippers when using multiple transportation and logistics providers, it is crucial to explore strategies that can help mitigate these issues. Consolidating providers and leveraging integrated logistics solutions can significantly enhance efficiency, reduce costs, and improve service quality. Here are some actionable recommendations for shippers looking to optimize their logistics strategies.
1.) Consolidation of Providers
By reducing the number of logistics providers, shippers can streamline their operations and reduce the complexities associated with managing multiple contracts and relationships. Consolidation enables shippers to improve coordination and ensure more consistent service quality across the supply chain.
2.) Single Point of Contact
Establishing a single point of contact within the logistics provider’s organization can simplify communication and coordination. This approach reduces the number of touch points and enhances accountability, making it easier to resolve issues and ensure seamless operations.
3.) Standardize Processes
Developing standardized processes and protocols for communication and coordination can reduce the likelihood of miscommunications and ensure a more consistent approach across the supply chain. Standardization can also facilitate smoother transitions between different stages of the logistics process.
4.) Training and Development
Investing in training and development programs for associates can enhance their ability to manage complex logistics operations effectively. Well-trained personnel are better equipped to handle coordination and communication challenges, reducing the risk of errors and delays.
5.) Performance Metrics and KPIs
Establishing clear performance metrics and key performance indicators (KPIs) for logistics providers can help ensure consistent service quality. Regularly monitoring these metrics allows shippers to identify and address performance issues promptly.
6.) Collaborative Relationships
Building strong, collaborative relationships with logistics providers can foster a culture of continuous improvement. Engaging providers in regular performance reviews and joint problem-solving initiatives can enhance service quality and drive operational efficiencies.
The Power of One
At Averitt, we understand the challenges of the modern supply chain. That’s why we offer seamless, integrated logistics solutions that eliminate the need to juggle multiple providers. Our approach is built around The Power of One, ensuring that you have a single point of contact for all your logistics needs. This strategy not only simplifies your operations but also enhances efficiency, reduces costs, and improves service quality.
At every turn in your supply chain, Averitt has you covered:
When it comes to achieving more, simplicity is key. By partnering with Averitt, you gain access to a comprehensive suite of services, seamless coordination, advanced technology, and consistent quality - all under one roof. Experience the Averitt difference and see how our integrated solutions can streamline your operations, reduce costs, and enhance your supply chain efficiency.
Watch The Short Video Below To Learn More About Our Power of One Approach!
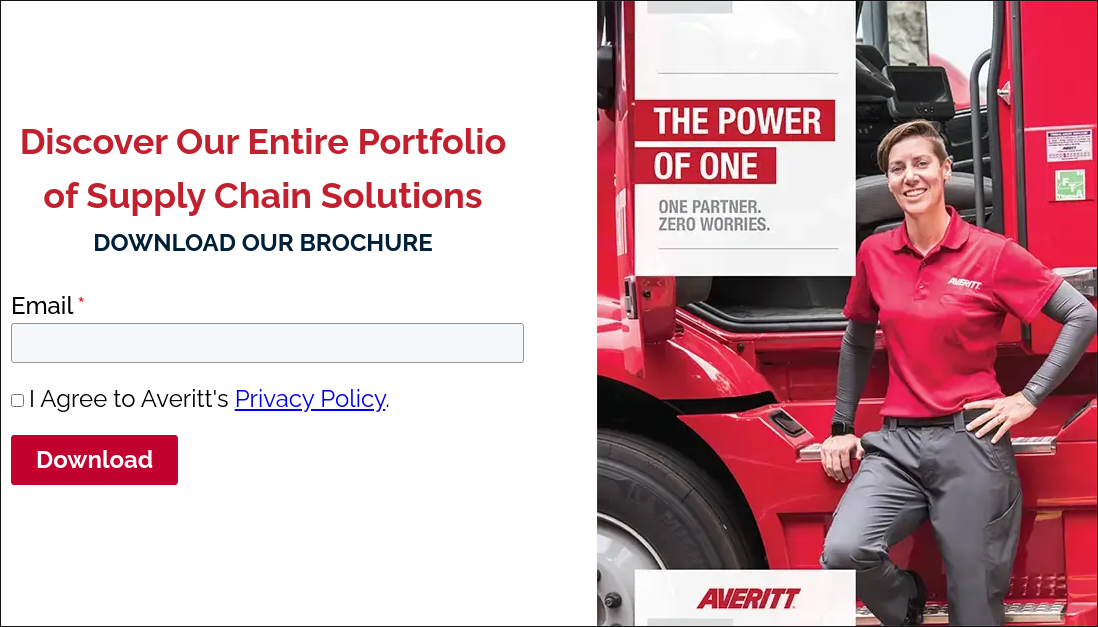